Shell & Tube Heat Exchanger
A Shell & Tube Heat Exchanger is the most widely used heat exchanger type in industrial applications, designed for efficient heat transfer between two fluids while maintaining physical separation. It consists of multiple heat transfer tubes enclosed within an outer shell, allowing one fluid to pass through the tubes while another circulates around them within the shell, facilitating thermal energy exchange.
At Rahavard Saei, we manufacture custom-engineered Shell & Tube Heat Exchangers tailored to various temperature, pressure, and process requirements. Our heat exchangers are built using high-quality metallic and non-metallic materials, ensuring durability, corrosion resistance, and maximum efficiency. We adhere to TEMA, API 660, and ASME Sec VIII standards, guaranteeing mechanical integrity and optimal thermal performance.
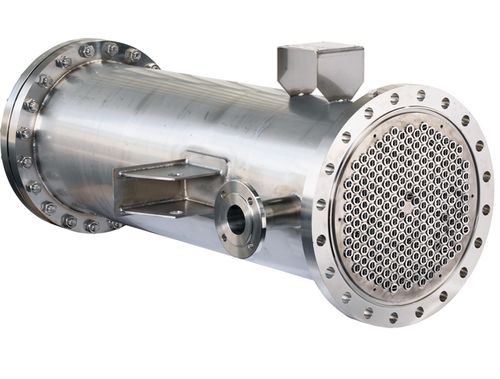
Key Features & Benefits
- High Thermal Efficiency – Optimized design for maximum heat transfer while minimizing energy losses
- Durable & High-Pressure Rated – Operates at pressures up to 6000 psi and temperatures ranging from -250°C to 800°C
- Custom Fabrication – Available in various sizes, tube arrangements, and materials to meet specific process needs
- Corrosion-Resistant Construction – Manufactured from stainless steel, titanium, nickel alloys, and other specialized materials
- Industry Standard Compliance – Designed and built to TEMA, API 660, and ASME Sec VIII standards
Mechanisms and Diverse Applications
Industries
Oil & Gas
Used in refineries, gas treatment plants, and petrochemical processing
Chemical & Petrochemical
Ensuring safe and efficient heat transfer for corrosive fluids
Food & Beverage
Hygienic design for pasteurization, sterilization, and temperature-controlled processing
Power & Energy
Enhancing steam cycle efficiency and waste heat recovery
Marine & Offshore
Providing durable cooling solutions for ship engines and offshore platforms
How It Works
A Shell & Tube Heat Exchanger consists of multiple heat transfer tubes, enclosed in a shell, where two separate fluids exchange heat without mixing. The tube-side fluid flows inside the tubes, while the shell-side fluid moves around them, enabling thermal energy transfer across the tube walls.
Key Components & Functions
- Heat Transfer Tubes – Carry one of the process fluids and provide the surface for heat exchange.
- Shell – Houses the tube bundle and directs the second fluid around the tubes for optimal thermal transfer.
- Front & Rear End Covers – Allow fluid entry and exit, ensuring proper flow management.
- Baffles – Direct the shell-side fluid flow, increasing turbulence and improving heat transfer efficiency.
- Tube Sheets – Securely hold the tubes in place and maintain separation between the two fluids.
During operation, the hot fluid transfers heat to the cold fluid through the tube walls, ensuring controlled and efficient temperature regulation. The use of baffles improves fluid contact with the tubes, maximizing heat exchange efficiency while preventing tube vibration and mechanical stress. Proper material selection ensures resistance to extreme temperatures, high pressures, and corrosive environments, guaranteeing long-term reliability and reduced maintenance costs.
Ready to Order? Get in Touch Today!
Looking for the right product for your needs? Get expert guidance and a customized quote by reaching out to us: